In industrial environments, where machinery operates in harsh and demanding conditions, every component plays a…
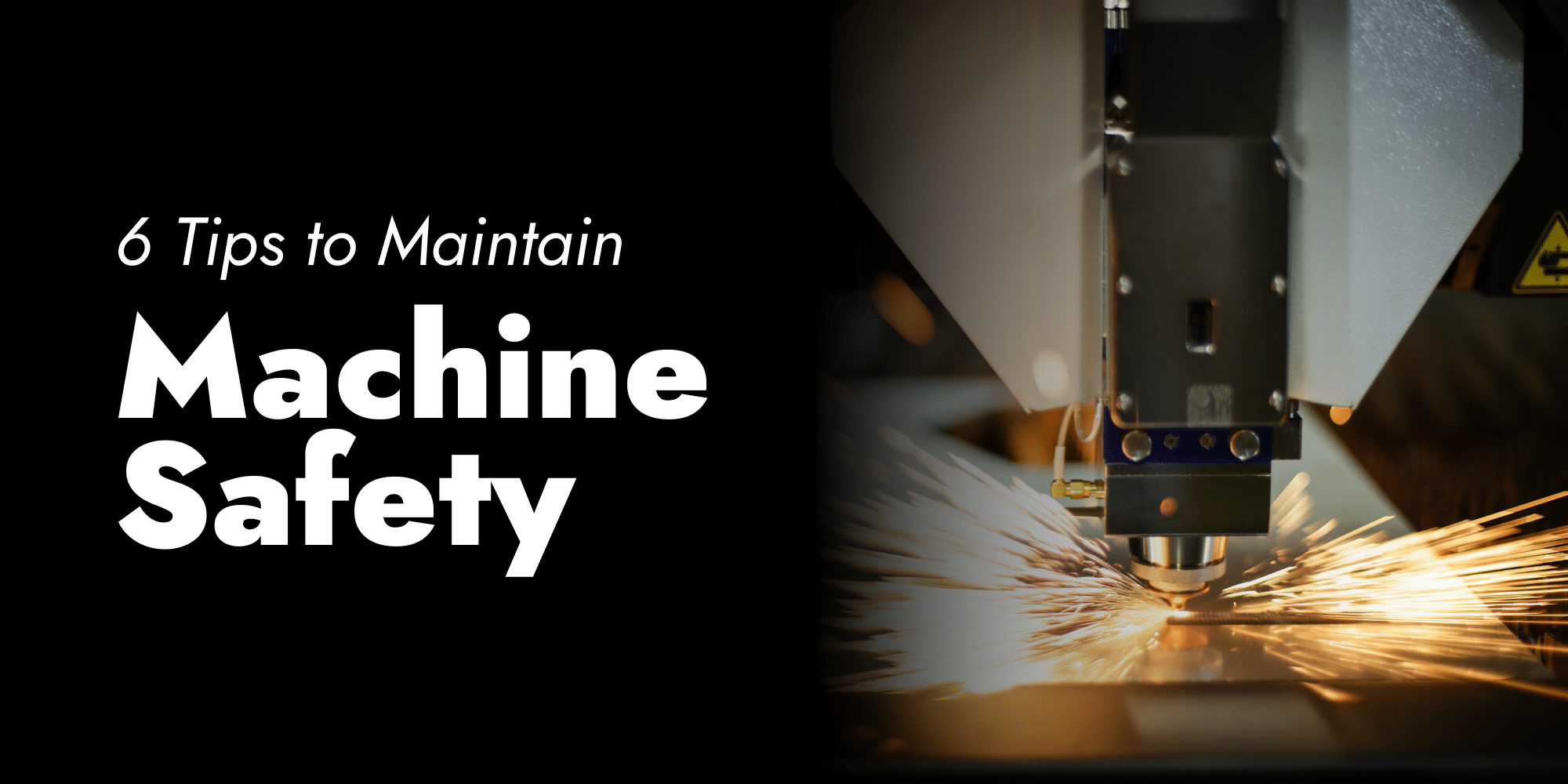
6 Tips to Maintain Machine Equipment Safety
Accidents and injuries caused by equipment malfunction can result in physical harm and significant financial losses. To ensure the well-being of workers and protect the bottom line, businesses need to implement effective strategies for machine equipment safety.
Importance Of Machine Safety Equipment
Machine equipment safety is crucial for legal compliance and business integrity. Neglecting it can result in severe injuries, legal costs, and damage to your reputation. Implementing effective safety measures protects employees, prevents equipment malfunctions, and maintains productivity. Prioritizing safety enhances your reputation, attracts top talent, and builds trust with clients and partners.
OSHA Rule For Machine Guarding
OSHA (Occupational Safety and Health Administration) has several rules and standards related to machine guarding to ensure workplace safety. One of the primary regulations concerning machine guarding specifies general requirements for all machines. Here’s a summary of key points from this regulation:
- Point of Operation Guarding: Machines must have guards to protect operators and other employees from hazards such as rotating parts, flying chips, and sparks.
- Power Transmission Apparatus: Guards must be in place to prevent employee contact with belts, gears, chains, and other moving parts that could cause injury.
- Nip Points: Guards must be provided to protect against hazards created by nip points, such as those formed where rotating parts move about each other.
- Additional Requirements: OSHA may specify additional requirements for specific types of machinery or equipment to ensure adequate protection.
Machine Safety Devices
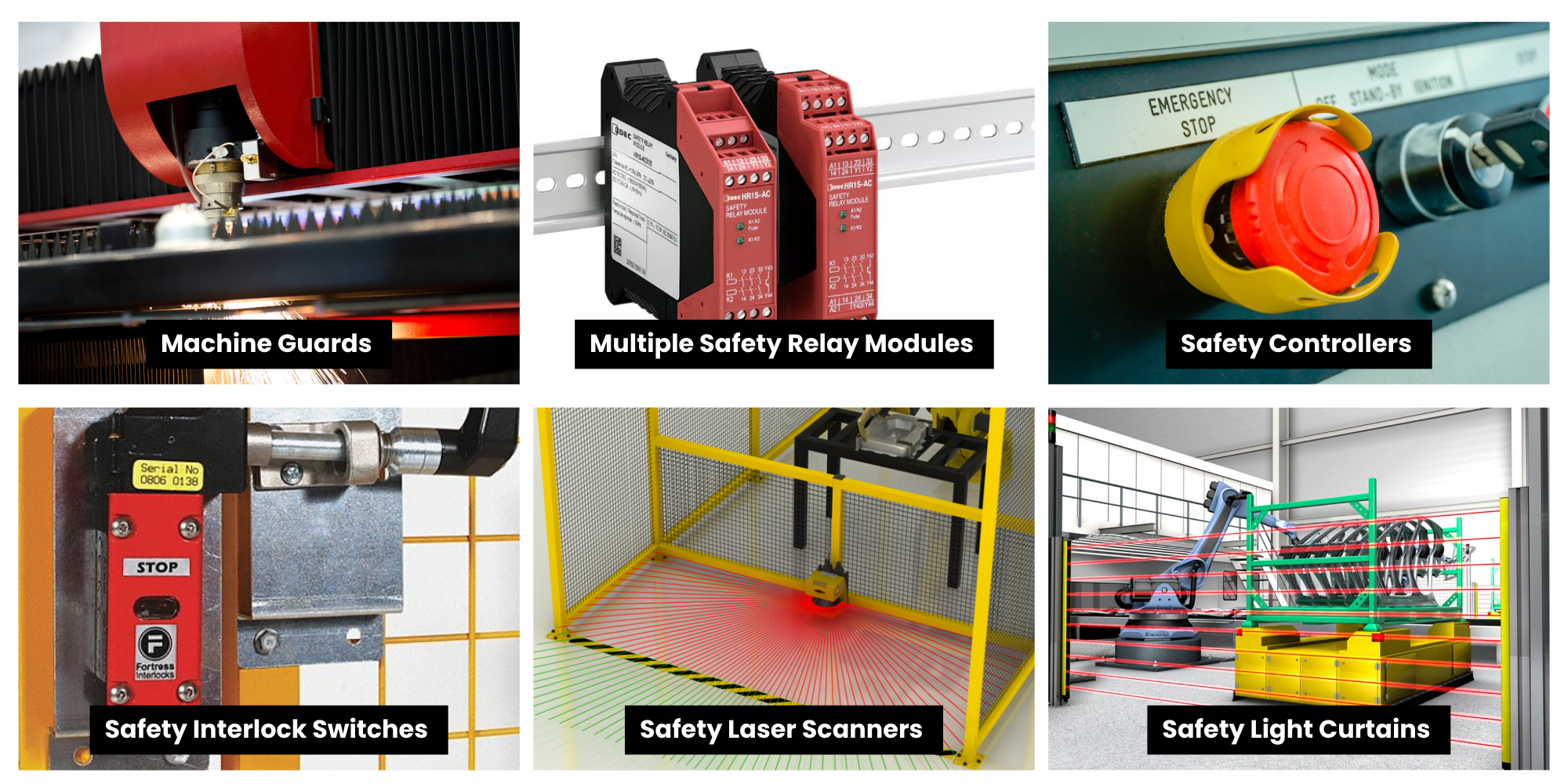
Machine safety devices protect workers and prevent workplace accidents in industrial settings. These devices are designed to mitigate hazards with machinery, such as moving parts, pinch points, and high-speed operations. Here are some of them:
Machine Guards
Machine guards, like flexible bellow covers, are an essential safety feature in any industrial or manufacturing setting. These guards are physical barriers designed to protect workers from the hazards associated with operating machinery. They are typically made of durable materials such as steel or plastic and are installed around the moving parts of machines to prevent accidental machine-guarding hazards.
Multiple Safety Relay Modules
These safety relays are designed to ensure the safe operation of machinery and equipment by monitoring various safety functions and responding accordingly. They are commonly used in emergency stop circuits, light curtains, safety gates, and two-hand control systems.
These modules’ main purpose is to detect potentially hazardous conditions and take appropriate actions to prevent accidents or injuries. The key advantage of using multiple safety relay modules is their ability to provide redundancy and reliability.
Safety Controllers
Safety controllers are designed to monitor and control safety-related functions, such as emergency stop buttons, safety gates, and light curtains. They are responsible for detecting potential hazards or unsafe conditions and taking appropriate actions to prevent accidents or injuries.
Safety controllers also provide logic and decision-making capabilities. They can be programmed to implement complex safety functions and interlocks to ensure certain conditions are met before proceeding. For example, a safety controller can be programmed to lock out a machine properly before allowing maintenance personnel to access it.
Safety Interlock Switches
These switches are designed to prevent accidents and injuries by interrupting the power supply or stopping the operation of a machine when certain conditions are not met. They are commonly used in industrial settings with a high risk of injury, such as manufacturing plants, warehouses, and construction sites.
Safety interlock switches prevent unauthorized access to dangerous areas of machinery or equipment. They are often installed on doors, gates, or panels connected to hazardous areas. When the door or gate is opened, the switch is activated and a signal is sent to the control system to stop the machine from operating.
Safety Laser Scanners
Safety laser scanners are designed to detect the presence of objects within a specified area and send signals to the control system to trigger appropriate safety measures. They use laser beams to scan the surroundings and create a protective field that detects any intrusion.
They are built to withstand harsh environmental conditions, dust, vibrations, and extreme temperatures. This ensures that they continue to function effectively even in challenging industrial environments.
Safety Light Curtains
Safety light curtains protect workers from potentially hazardous areas by creating an invisible light barrier. They consist of a transmitter and receiver mounted on opposite sides of the area that needs to be protected. When an object or person interrupts the light beam, the curtains immediately signal the machine, causing it to stop or slow down, preventing accidents or injuries.
They can be easily installed and adjusted to fit different sizes and shapes of machinery or work areas. Safety light curtains can also be integrated with other safety devices, such as emergency stop buttons and safety interlocks, to provide comprehensive protection for workers.
Maintain Efficiency And Productivity With These Safety Tips
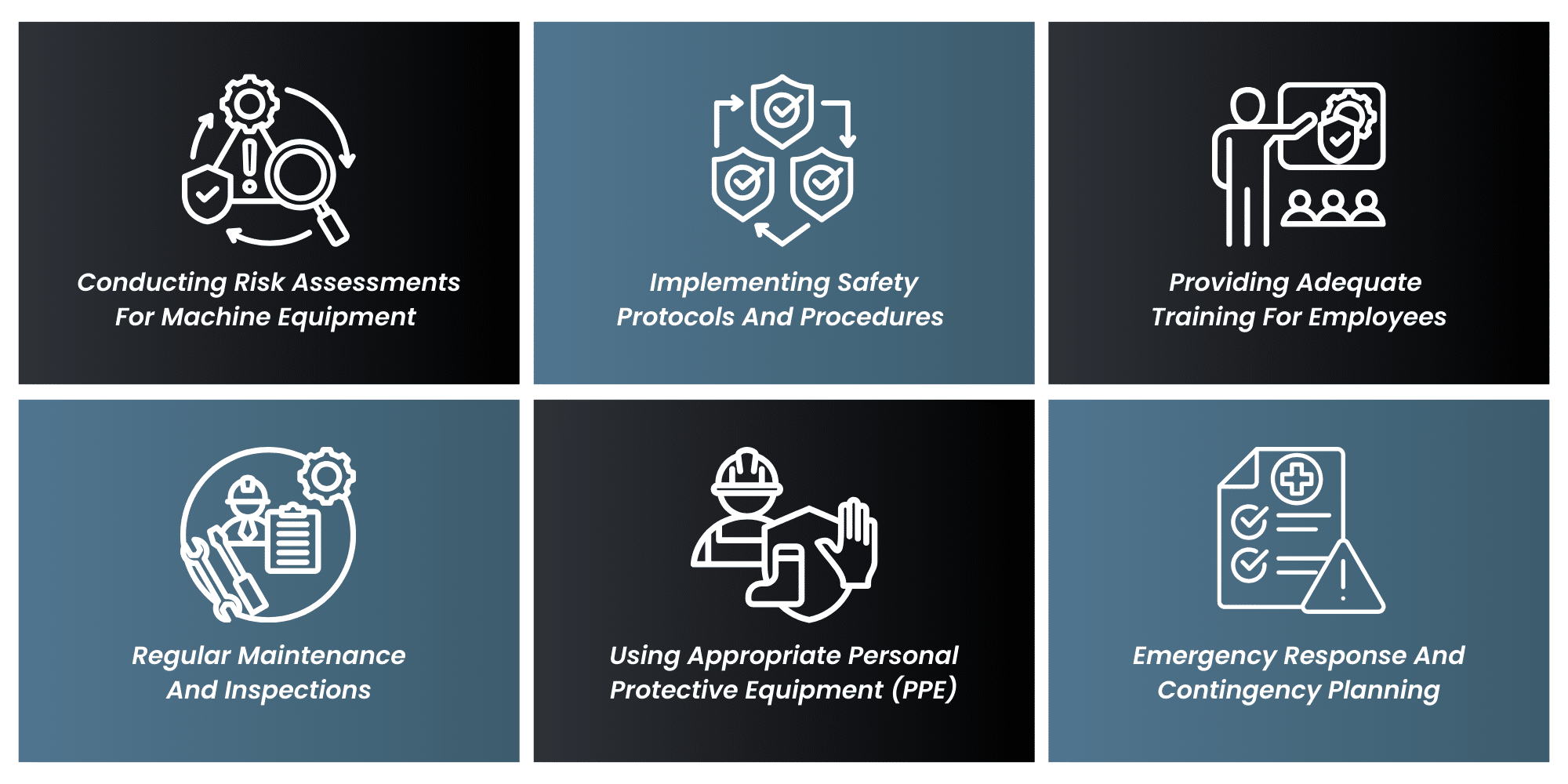
Ensuring machine equipment safety is paramount in any workplace to prevent accidents and injuries. Here are six tips to help maintain machine equipment safety:
Conducting Risk Assessments For Machine Equipment
A risk or hazard assessment is a systematic process of identifying hazards, evaluating potential risks, and implementing control measures to minimize or eliminate risks. Conducting a risk assessment for machine equipment is a critical step in ensuring the safety of workers and preventing accidents.
The risk assessment process typically involves the following steps:
- Identifying all potential hazards associated with the machine equipment.
- Once hazards are identified, assess the risk associated with each hazard.
- Based on the risk assessment, appropriate control measures should be implemented.
- Risk assessments should be reviewed periodically to ensure their effectiveness and update them as necessary.
Implementing Safety Protocols And Procedures
These protocols serve as guidelines that employees can follow to ensure their safety and the safety of others. The first step in implementing safety protocols is to develop a safety program outlining the company’s commitment to machine equipment safety and providing clear employee expectations. This program should include information on hazard identification, risk assessment, safety training, and reporting procedures.
Specific safety protocols and procedures should be established for each machine equipment type. These protocols should outline safe operating procedures, maintenance requirements, emergency shutdown procedures, and other relevant safety guidelines.
Providing Adequate Training For Employees
Proper training is a fundamental component of machine equipment safety. Employees who operate or work with machine equipment should receive comprehensive training on safe operating procedures, potential hazards, emergency response protocols, and proper use of personal protective equipment (PPE).
Training programs should be tailored to the specific machine equipment used and the tasks performed by employees. They should cover equipment operation, maintenance, lockout/tagout procedures, hazard identification, and emergency shutdown protocols.
Training should be provided to new employees before they begin operating or working with machine equipment. It should be periodically held for existing employees to reinforce safe practices and update them on equipment or safety regulations.
Regular Maintenance And Inspections
Businesses should establish a preventive maintenance program that includes regular inspections, cleaning, lubrication, and adjustment of machine equipment. This program should be based on manufacturer recommendations, industry best practices, and regulatory requirements.
Inspections should be conducted by qualified personnel knowledgeable about the specific equipment being inspected. They should check for signs of wear and tear, loose or damaged parts, proper functioning of safety features, and any potential hazards. Inspections should be documented, and any issues identified should be addressed promptly.
Regular maintenance should be scheduled and performed according to the manufacturer’s recommendations. This can include changing filters, replacing worn-out parts, and ensuring proper calibration and alignment. Maintenance should be documented to keep track of performed tasks, identify trends in equipment performance, and plan for future maintenance needs.
Using Appropriate Personal Protective Equipment (PPE)
PPE should be considered the last line of defense after other control measures. It should not be relied upon as the sole means of protection. Instead, it should be used with other safety protocols and procedures.
When selecting PPE, businesses should consider the hazards associated with their machine equipment and the tasks performed by employees. The chosen PPE should provide adequate protection against identified risks and be comfortable for employees.
Employees should be trained on the proper use, care, and maintenance of PPE. They should understand when and where to use specific types of PPE, how to fit and adjust the equipment, and how to inspect and clean it.
Emergency Response And Contingency Planning
Emergency response plans should outline procedures for various scenarios, such as equipment malfunctions, fires, chemical spills, or medical emergencies. These plans should specify evacuation routes, assembly points, emergency shutdown procedures, and the roles and responsibilities of employees during an emergency.
Employees should receive training on emergency response protocols and be familiar with the location and proper use of emergency equipment, such as fire extinguishers or first aid kits.
Businesses should also establish communication channels for reporting emergencies and ensure employees know how to activate these channels. This allows for prompt response and coordination during critical situations.
Protecting People and Machines With Years of Technical Experience – OTEGO
Machine equipment safety is not an option but a necessity for businesses in today’s industrial landscape. Implementing the essential strategies outlined in this guide can create a safe working environment, protect your employees, and avoid costly accidents and legal consequences.
OTEGO is a leading technical textile solution company that upholds this working principle through our global and local representations. We specialize in technical fabrics for applications requiring abrasion resistance, flame & heat protection, and release coatings. You can count on us to help you improve productivity and contribute to your business development via our customized solutions.
Connect with us today to learn how we can help you with your technical fabric issues and requirements.