Heat ducting plays a crucial role in many industries by controlling and directing hot air,…
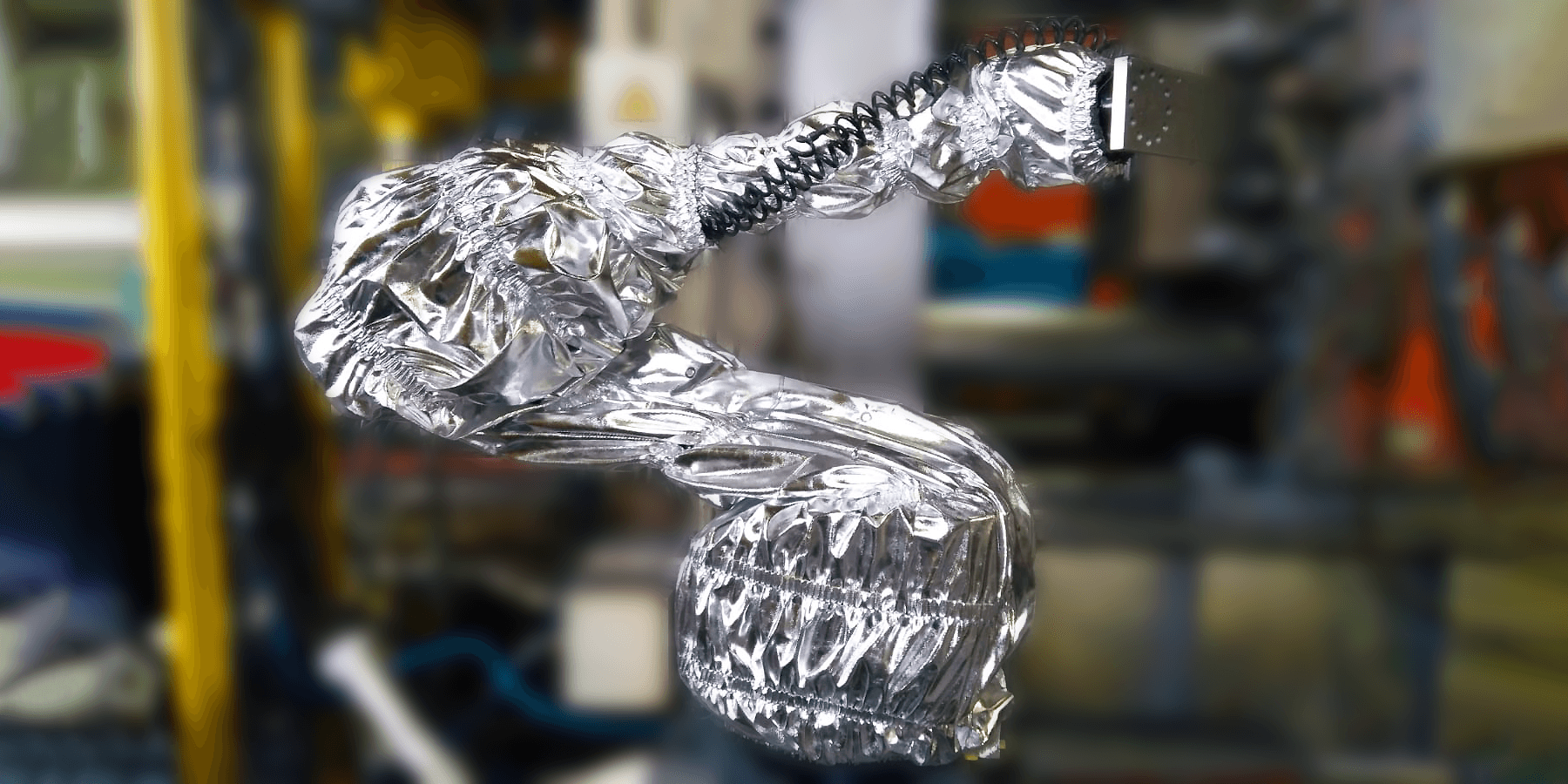
Impact of the robot covers on productivity
Automation :
Industrial automation is accelerating on a global scale. Compared to human, robots allow companies to reach much higher efficiency, performance and uniformity for a given task. They have the ability of working in dangerous environments, and execute the same moves repetitively without getting tired nor lose precision.
Performance parameters :
To ensure a high productivity of the automation, plants measure a robot performance through 3 KPIs that determine its ROI:
- The MTBF aka Mean Time Between Failure : the time when a robot is operating normally.
- The MTTR aka Mean Time To Repair : the time a robot needs to be fully repaired and operational.
- The Down Time : the time when a robot is unable to pursue its tasks.
Why to protect robots :
It is important to prevent failure that could ruin a robot performance and the investment it represents. That is why it is necessary to use the appropriate protection against harmful factors. It reduces both risks of failure (reducing MTTR and Down Time) of the robot and extend its lifespan (increase MTBF).
Risk Factors :
The following list is made of factors that might provoke damage and even failures on the long run if they are left unattended.
Dust & Particles :
Machining robots, used in heavy industry, are often exposed to dust and particles generated from the material they process. Solid particles or splinters often lodge inside the equipment, creating abrasions and obstructions, that might clog or jam mechanisms, and damage the robot. Dust mixed with process fluids can also stick to captors and sensors misleading the system and forcing it to shut down the unit.
Molten Metal & Welding Sparks :
Welding robots or foundry handing robots are exposed to hot molten metal projections that agglomerate in time. Those projections could limit or disturb the range of motion of the robot arm and make it unable to operate.
High Level of Radiant Heat :
Long exposure of high level of radiant heat damage the robot by fusing, melting, or solidifying mobile elements. It also affects unprotected electric wiring and electronics parts by melting them.
Static Charge Build Up :
An accumulation of micro particles in the robot provokes a static charge build up, leading to arc flash hazards and sparks, particularly dangerous in explosive environments.
Different environments, different risks :
Foundry
Handling robots – Molten steel/Aluminum handling.
Protective cover is used to reflect radiant heat coming from the oven and protect the robot from projections and radiant heat. Without a reflective aluminized protection different parts that are close to the molten metal may bend with the stress due to the heat and the weight.
Risks Factors :
- Molten metal splash on the robot
- Radiant heat coming from the oven
- Convective heat coming from the bucket of molten metal
Forge
Handling robots – High temperature metal parts.
A very aggressive lubricant is used to help extraction of the part from the mould. These lubricants can be charged with graphite. Graphite can be abrasive for certain chemistries. In addition of the radiant heat, the cover needs to also protect the robot against these lubricants.
Risk factors:
- Metal projections
- Radiant heat coming from the material and the oven
- Convective heat coming due to the proximity with the oven
- Abrasive lubricant projections from the mould
Sandblasting
Sandblasting robots – Extremely abrasive environment.
Sandblasting robots are quite difficult to protect for long term as they dispatch highly abrasive materials. Due to their size, the sand and dust particles that are blown out for sanding get into the wrists and mechanisms of the machine. As a result, they may provoke failures. Normal materials get worn out very fast with these kinds of conditions, that is why the cover needs to be made from an abrasion resistant coated fabric.
Risk Factors:
- Abrasive sanding material and dust
Machining Robots/Machined parts Handling Robot
Robot covers for parts handling are inflated continuously. In this case, it is usual for the machine to face an environment full of thin metal particles and cutting oil splashes.
Unprotected, the robot pivot connections can get contaminated by thin metal particles, dusts or even machining chips. Moreover, cutting oils can damage the robot and even the robot cover if the fabric is not appropriate.
For instance, PVC covers are in this case prohibited as the plasticizers contained in the PVC will react with the oils and the cover will get stiffer with time.
- Abrasive dust and particles.
- Corrosion due to cutting oil splashes
Food industry
Machine in direct contact with food.
It is important that the machine does not contaminate the food of the production line, that is why the robot’s cover needs to be airtight and waterproof. To minimize any risk of contamination, the covers are inflated continuously and washed regularly. Two majors requirements exist in this case: the needs for the cover to be PVC free, and necessity of food grade protection.
Risk factors:
- Food contamination
Who are we ?
We have developed a full range of materials to match the specific requirements for industrial robot coverings. Please feel free to contact us if you need more information.