In industrial environments, where machinery operates in harsh and demanding conditions, every component plays a…
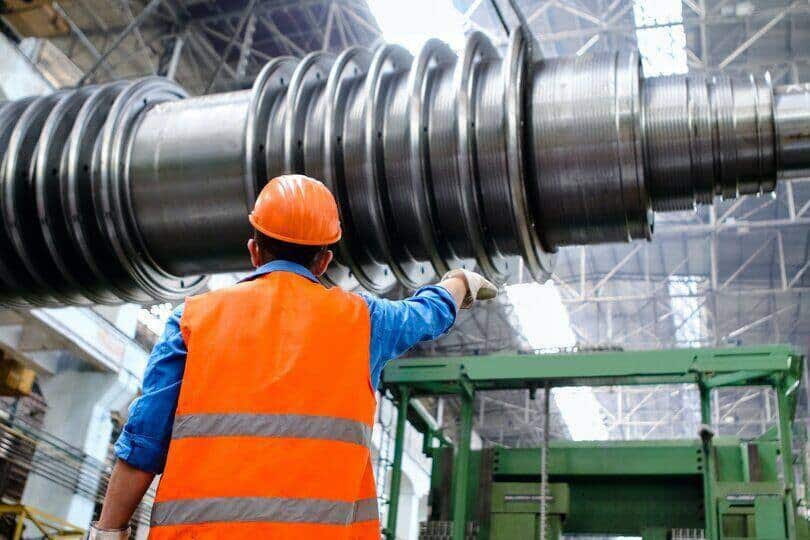
Growing Trend In Using Assembly Robots In Heavy Industries
The usage of robots in heavy industries has been increasing over the years. The logic behind this is that robots are often able to perform required tasks in these industries with greater accuracy and speed than humans. As a result, companies are relying more on robots to help with tasks such as welding, fabricating, and assembling. This blog post will explore why the usage of robots is on the rise in heavy industries and how they benefit these industries.
Trend for automatization and the use of robots in the manufacturing industry
The manufacturing industry is one of the most important industries in the world. It is responsible for the production of goods that are used in our everyday lives. In recent years, there has been a trend toward automatization and using robots in the manufacturing industry. This is because robots can carry out tasks more efficiently than humans can without suffering from fatigue and inconsistencies. As a result, the use of robots can help to increase the productivity of a company. With more time available, humans can focus on other tasks that need personal intervention as this cannot be easily replaced by robots.
Assembly robots are used in the manufacturing process of various products. As the robotic assembly system is faster than the human assembly process, it can help to improve the production rate.
There are many benefits of using robots in heavy industries. Below are some of the biggest advantages that they can bring to production:
Carry out tasks more efficiently than humans can
Robots are generally more efficient than humans, especially when the tasks are repetitive. This means they can multiply the productivity of a company without the risk of decreased quality due to exhaustion.
An assembly line robot can do the work of several human workers. This can help to free up human workers to do other tasks. While robots work on the mundane tasks, humans can divert their focus on other things that need their attention.
Assembly line robots differ not only in their speed but also in their accuracy. Suppose that a company is making a product that requires precise measurements. In that case, they would need to use a more accurate robot to avoid any mistakes.
Can work in hazardous environments
Some environments are too dangerous for humans to work in. For example, working in a nuclear power plant is very dangerous. However, some robots can work in these environments without any problems. This is because they are not affected by hazardous conditions. They can also perform tasks that are too difficult or dangerous for humans. For example, a robot could be used to clean up a nuclear power plant after a disaster.
When an assembly robot is used in a factory, the working conditions are much safer for the workers. Many times in a factory, the workers are exposed to loud noises, fumes, and dangerous chemicals. When robots are used in these factories, the workers are not exposed to these conditions.
Work for longer hours without getting tired
Robots can work longer hours without getting overworked even when operating in extreme conditions. They are mostly used in heavy industries such as automobile manufacturing, which are used for welding, painting, and assembling cars. A robotic assembly line can work 24 hours daily, which is impossible with human workers. This increases the factory’s production capacity and reduces the cost per unit.
Help to improve the quality of products
Robots can help to improve the quality of products because they can consistently do the same thing without suffering from fatigue. They can also be programmed to do a task in a certain way. For example, a welding robot can be programmed to weld two pieces of metal together in a specific way. This ensures that the welding is high quality and that the metal is not damaged. In advanced manufacturing, robots are increasingly used to carry out quality control tasks.
Reduce the cost of production
The use of robots can reduce the cost of production. This is because they can work for longer hours and do not need breaks. This helps to reduce the overall cost of production. If assembly operations are automated using robots, the need for workers is reduced. This can lead to savings on labor costs.
How are robots used in heavy industries?
Now that we know the advantages of using robots in heavy industries let’s look at how they are used.
Food industry
Fig. 2. Robots are also used in the food industry
In the food industry, robots are used for packaging, inspection, and sorting tasks. For example, the Coca-Cola Company uses robots to inspect bottles for defects and to sort them by color. Just as the artificial intelligence in robots is constantly improving, so is their ability to handle delicate tasks such as these. The Arm Institute, an organization that promotes the advancement of robotic technologies, explains:
“One major advantage that robots have in the food industry is their dexterity. For tasks such as packing or stacking, which require a high degree of accuracy, robots can be more precise than humans. In addition, thanks to their computational power, robots can be programmed to complete these tasks faster and more efficiently than humans.”
Automotive industry
In the automotive industry, robots are used for welding, painting, and assembling. For example, Toyota Motor Corporation uses robots to weld the bodies of its cars. This is because robots can weld more quickly and precisely than humans. Materials science that studies metals and their alloys are also used in the automotive industry. This is because metal alloys make car parts such as engine blocks and transmissions.
When the industrial robot is used in the automotive industry, it helps to increase the productivity of the manufacturing process and also improves the quality of the final product. The Four Axis Scara robots are used in the automotive industry for welding, fabricating, and other manufacturing processes.
Steel industry
Tasks in the steel industry, such as casting, hot rolling, and cold rolling, are completed by robots. For example, the South Korean steel company POSCO uses robots to cast molten steel into ingots. This is because robots can handle the high temperatures and heavy weights involved in this process.
Metallurgy which involves the study of metals and their alloys is also used in the steel industry. This is because metal alloys make steel products such as pipes and wires. Usually, the alloys used in steel products are iron, carbon, and chromium.
Unlike other industries, the steel industry uses a lot of heavy machinery. This is because the process of making steel products is very energy-intensive. For example, the process of hot rolling steel involves passing the metal through a series of rollers that are heated to high temperatures. This process is known as hot working. The high temperatures make the metal easier to shape.
Mining industry
Fig. 3. The mining industry heavily relies on robots in harvesting and processing minerals
Mining is dangerous because it involves working in underground tunnels and caves. Robots are used in the mining industry to do tasks such as exploring mine shafts, drilling, and blasting. For example, BHP Billiton, an Australian mining company, uses robots to explore mine shafts for minerals. This is because robots can enter these areas without risking the safety of human workers. The geology that involves the study of rocks and minerals is also used in the mining industry. This is because rocks and minerals are mined for their valuable metals and minerals.
Construction industry
The construction industry uses industrial robots for bricklaying, pouring, and framing. For example, KUKA, a German robotics company, produces robots that are used to lay bricks. This is because robots can lay bricks more quickly and accurately than humans.
Civil engineering, which involves the design and construction of infrastructure, is also used in the construction industry. This is because infrastructure, such as buildings and bridges, needs to be built. Robotic technology is used in the construction industry to build this infrastructure. For example, Boston Dynamics produces robots that can be used to build bridges.
OTEGO – Technical Fabrics for Protecting Robot Assets
When working with heavy industry and machines, it’s important to have the best possible fabric solutions to protect people and assets. That’s where OTEGO comes in – we provide heat-protective fabrics, protective covers, seam sealing tapes, and other specialized fabrics that can be used to shield assets from damage.
With our knowledge and expertise, we can help ensure that your assets maintain their integrity by protecting them from harmful elements and activities. The robot covers and sleeves that we manufacture at OTEGO are made of high-quality, durable materials that can withstand the rigors of industrial use. We understand that when it comes to working with heavy machinery, there is no margin for error – which is why we take pride in providing the best possible fabric covers.
When you work with OTEGO, you can be sure that you’re getting the best possible solution for your needs. We can create customized fabric covers for your assembly and advanced robotics assets (like laser cutting tools) to ensure they maintain optimum operational function even in extreme environments.
Contact us today to learn more about what we can do for you.