Carbon emissions have been steadily increasing in the past few decades, and there are serious…
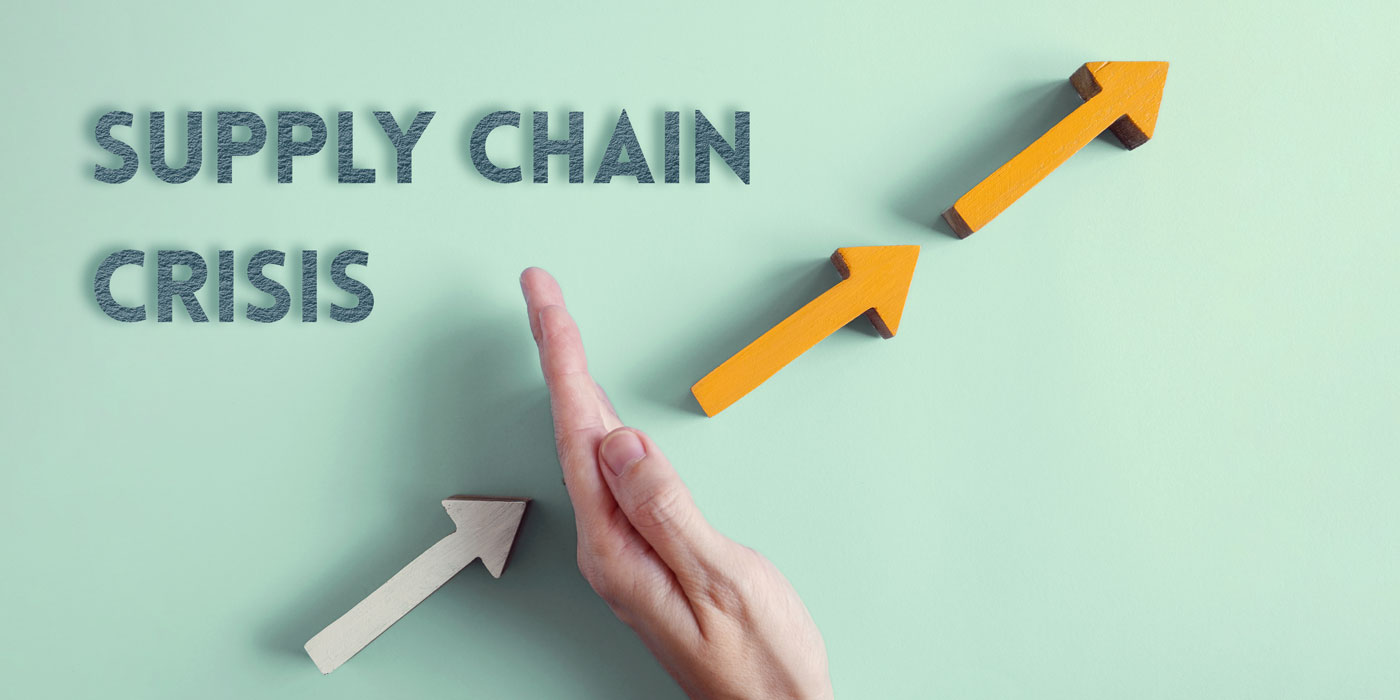
Global Textile Shortage – Impact On Businesses And End-Users
The eruption of the COVID-19 pandemic created a whirlwind that threw the global economy in a tailspin. This resulted in supply shortages that impacted countless businesses around the globe. Many international corporations, including textile companies, were affected by the pandemic as the domino effect rippled throughout the global supply chain.
Global Logistics Issue Due to COVID
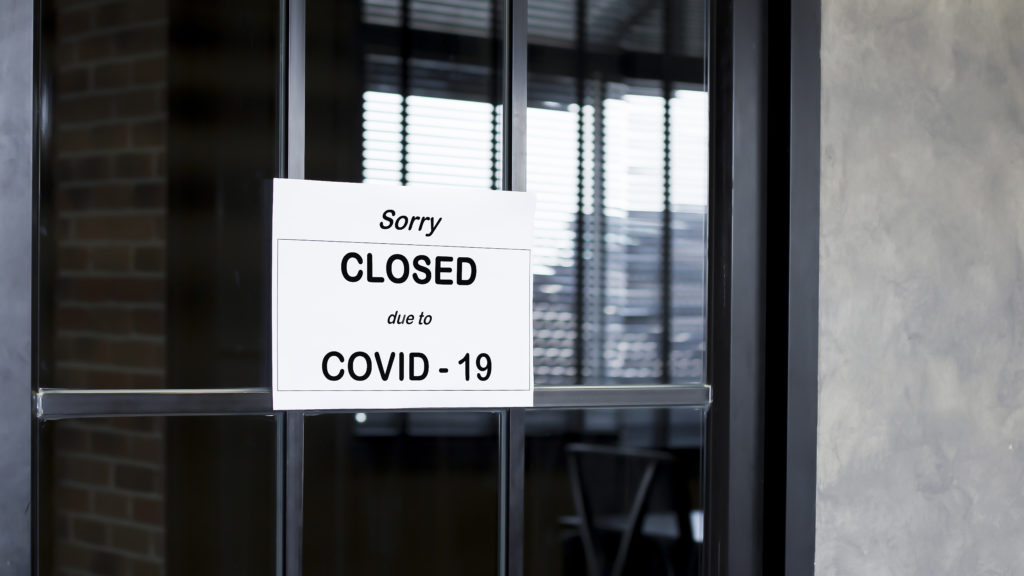
As the virus spreads, key exporters like Brazil, Mexico, India, and China, and importers like the European Union and the US, face worsen freight constraints on the already troubled logistics chain. Disruptions in manufacturing, growing backlogs in container ports, and the shortage of drivers further aggravated the difficulties in maintaining the supply chain.
Major industries including electronics, automotive, consumer goods, pharmaceuticals, and medical equipment and supplies were affected by the restrictions and bottlenecks in the supply chain. The interconnectivity of supply chains also affected the textile and chemical industries. The textiles, clothing, leather, and footwear (TCLF) industries suffered from factory and shop closures, a drop in sales, and sourcing difficulties.
From a logistics perspective, textile production is time-sensitive, especially when industrial textiles are needed for the production of PPEs. The demand for plastics, textiles, and medical supplies drastically rose and was prioritized for transportation over other goods.
All these events resulted in huge backlogs that pressurized supply chains worldwide. While some countries recovered earlier, many remained in lockdown. The discrepancy caused an imbalance in the supply and demand distribution as recovering economies were being slowed down by their needs from nations that were still at the peak of combating the virus.
Short-Term Effects of Supply Chain Problems
-
Longer lead time
Depending on a single source for raw materials proved to be disastrous to many organizations. Logistic constraints and transport regulations led to shipment delays that lasted longer than expected. Ships remain anchored for weeks on major ports as increased shipping volumes cannot be processed by the limited personnel capacity. The whole situation caused longer lead times for the manufacturing and retail industries.
-
Price increase
Because of the logistics problem, manufacturers and retailers weren’t able to adjust in time to bridge the gap between supply and demand. With the high demand and low supply of materials, price increases became inevitable. It was thought that the supply shortage would dissipate as rising prices suppress demand, eventually resulting in market equilibrium. However, prices remain high as supply shortages persist, all while having steady demand.
Long-Term and Hidden Effects of Logistics Issues
-
Supply instability
With the gap between supply and demand for materials, suppliers often choose more favorable clients, especially those with larger orders. This helps them recover logistics costs better, move products more efficiently, and serve clients with bigger target markets.
Smaller clients have to wait longer to replenish their stock. Some are pushed to look for alternative suppliers even in exchange for higher costs. Businesses with insufficient resources to continue operations are forced to cut their workforce or worse, close shop.
-
Shifting of production capacity away from niche markets
Confronted with raw materials shortages, some manufacturers choose to discontinue certain ranges of products deemed not profitable enough to focus on their core business, often at the expense of their customers that are left stranded.
-
Quality drop
To keep up with the demand and maintain operations, businesses are forced to churn out products faster. Oftentimes, the rushed production of goods results in lower quality products. It has been challenging for businesses to maintain operations, with many of them resorting to layoffs. Companies running with a reduced workforce – especially those in the service business – have felt the impact of operating with limited manpower in the quality of service they provide to end-users.
-
Moving production sites closer to consumers
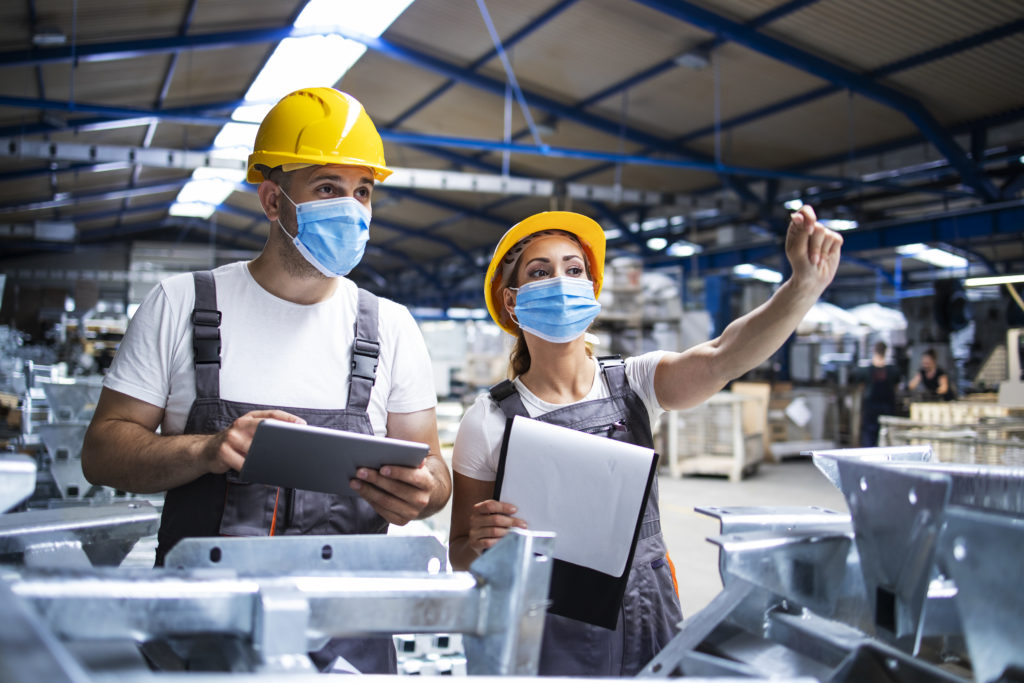
Glocalization is the portmanteau of the terms ‘globalization’ and ‘localization’. It is used to describe products or services distributed on a global scale but has the flexibility to cater to the local market and end-users. It focuses on thinking on a global scale while also acting locally to meet the needs of the target market. Products and services that have been “glocalized” are generally more meaningful to end-users because they’ve been customized to meet local needs.
Glocalization must be taken to the next level to overcome the vulnerabilities exposed by the pandemic. Sourcing and manufacturing need to become more local and redundant to break through the limits of thin margins and just-in-time production. Not only does this reduce the risk of encountering logistics issues but also lowers the cost of production and delivery from a long-term perspective.
Aside from finding alternative suppliers, organizations are considering using local resources and talents as part of the next level of glocalization. Instead of simply importing goods from certain regions, managers are looking into producing a substantial portion of merchandise within the region where they’re consumed.
Branching out the operations of industry players from developed countries improves their resilience and flexibility against crises. This gives them a competitive advantage in the industry while spurring economic development in countries that have suffered from factory closures.
OTEGO: Making a difference by being there for our customers
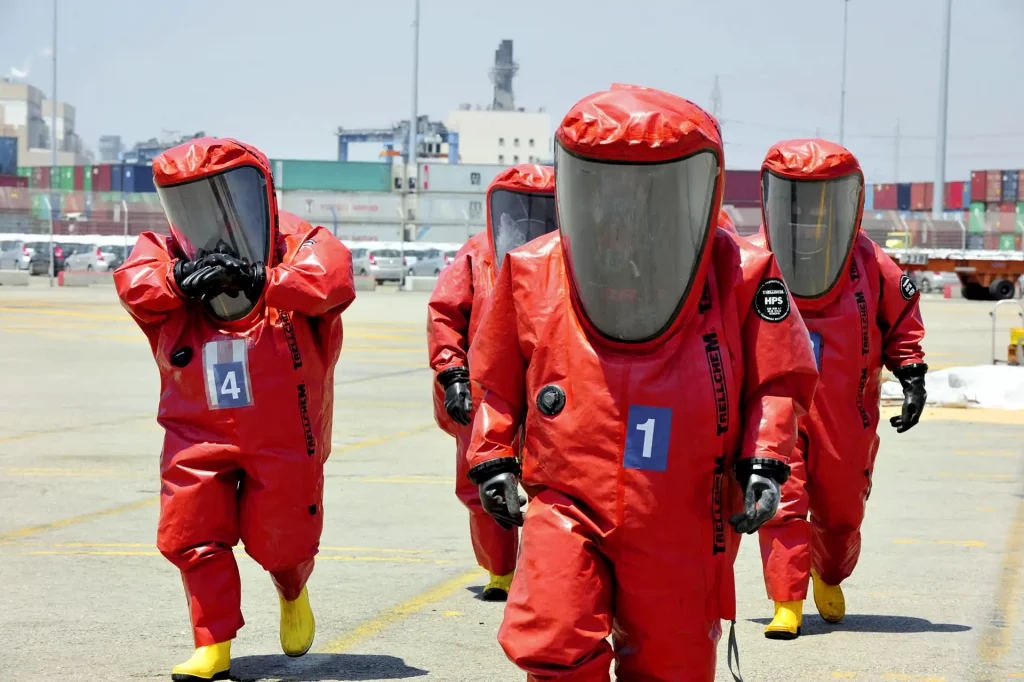
Otego is no different from the many companies around the world and is equally impacted by these unprecedented shortages that followed the COVID crisis. However, we believe that this is the opportunity to show our resilience and our commitment to support our customers around the world by providing them the textile they need, no matter their size or their applications. We do our best when it comes to managing supply chain risk to ensure the best lead time for our customers. Building a network of suppliers, considering alternative logistics solutions, and managing long-term stockpiles are the keys to future-proofing the business for similar crises that might happen in the years to come.
Aside from manufacturing high-quality liners, ducting, seam-sealing tapes, protective covers, and heat-protective and heat-resistant fabrics, we also believe in satisfying our end-users.
We’ve built an ecosystem that spans several countries worldwide. This has provided us with the resilience against shortages and logistics problems that became the highlight since the pandemic began. We’ve managed to stay operational despite the global shortage that hit the industry. Our customers can count on our support as we’re here to meet their demands.
If you’re having problems with your current supplier, consider switching to Otego. Contact us for industrial textile solutions.