When it comes to the aviation industry, every component must be designed and chosen with…
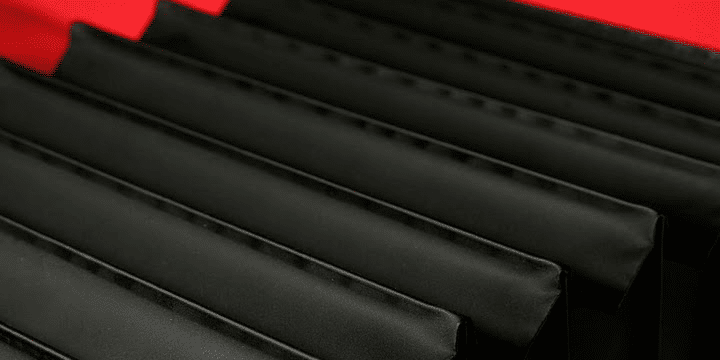
The common issues with flexible bellow covers and how to prevent them.
Metalworking is one of the key industries in our modern society and consists on processing metals to produce parts and structures for a wide array of industries such as aircraft, automotive, etc.
It generally involves high precision machine tools, highly skilled operators, and delivery deadlines.
The challenges a metalworking engineer faces, are multiple and can come from mechanical failures due to the machine, failures due to temperatures, due to the materials he is working on.
Each issue will slow down or stop the production, impacting your OEE (Overall Equipment Effectiveness).
Bellow cover could be one of them. To avoid this, we will try to list up the common bellow failures that could happen and how you could prevent it, so bellow is one less problem you have to care about.
Flexible Bellows covers common failures:
Rupture, breakage:
Flexible bellows are submitted to a lot of mechanical stress. Overtime, the tension could lead to apparition of pinholes (small holes at the folding points where the tension is highest). The pinholes indicate that the cover is wearing out and will progressively expand with time. Depending on the requirement of the process, a replacement can be scheduled sooner or later, but pinholes issues seldom lead to a machine shutdown. However, in the eventuality of a bellow breakage, the impact on the production can be more important. Exposure to coolant fluids could alter the materials of the cover causing it to lose flexibility. PVC materials for instance will tend to become stiffer and less resistant to mechanical stress. Once it is weakened, it may break at folding lines more easily.
How to prevent it?
Make sure to choose a coolant resistant material for your bellows, so the cover is not chemically affected and remain supple. It is best to share what kind of coolant you are often using with your bellow maker to make sure they select the right material. Select high tenacity fibers for big size bellows for a better tensile resistance.
Derailing:
Flexible bellows are lightweight and more compact than telescopic steel covers. They can easily fit horizontally, vertically, or even upside down to the machines to protect the linear motion guides from chips and scraps. They are usually fixed and hold in place by mobile PVC plates to which they can be stitched, glued, or welded. Derailing can occur if the material is too supple and loose shape or detach from the plates.
How to prevent it?
Choose a material that has a good folding memory, so the cover does not run out of its path. Make sure also that the material has a good High Frequency welding adhesion (HF Welding) with the PVC plates, so it does not detach unexpectedly.
Surface damages:
Bellow covers can be exposed to abrasive debris (coming from the process or from the cutting and grinding oils). Those abrasive residues in addition to repeated movement will damage the cover overtime. Delamination can also occur in between folds due to the vacuum peeling effect of some coolant. The liquid mixed with fine particles can stick the folds together and rip off the coating if left overnight.
How to prevent it?
Opt for hard coated fabrics (PUR) over soft ones (PVC, TPU) which will be more exposed to such damage. Try to clear out the debris regularly to avoid letting it “sawing” through the fabric. Also prefer fabrics with slight “emboss” over flat ones to break the “vacuum peeling” phenomenon.
Piercing and holes:
At high speed, scraps can puncture the bellow cover.
How to prevent it?
For application requiring high impact resistance, it is recommended to use para-aramid based fabric or to choose hybrid bellows covers, reinforced with steel lathes.
Who are we?
OTEGO is specialized into technical fabrics for flexible bellow covers solutions.
Please feel free to visit our page dedicated to bellow for more information.