Heat ducting plays a crucial role in many industries by controlling and directing hot air,…
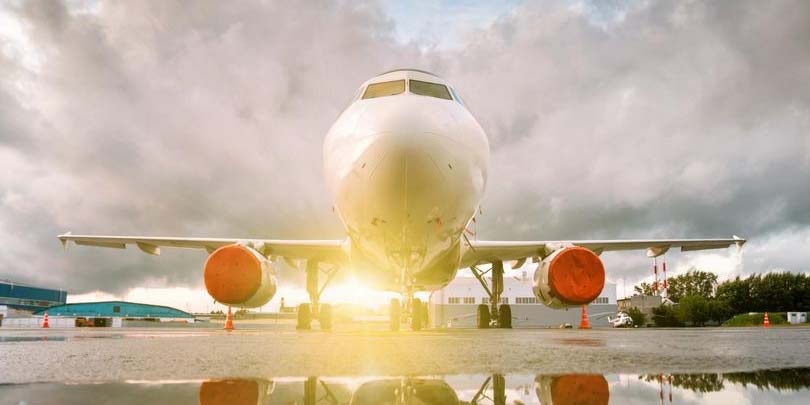
Protecting Aircraft During Forced Storage
The Covid-19 Pandemic at its height was unprecedented in scope and scale. The entire world was shut down and entire industries ground to a halt. With everyone under lockdown, the airline industry was forced to park their planes into storage. Images of entire aircraft fleets lined up on the runway went viral as airlines were continuously grounded. It is only recently that the skies are filled again with the roaring jet engines of airplanes.
The grounding of entire aircraft fleets presented a major logistical challenge. Airports were running out of space to store planes safely and aircraft manufacturers like Boeing and Airbus had to hold back airplane deliveries and thus adding to the bottleneck of airplanes strewn across parking lots.
This begs the question, how does one protect the most critical part of a plane which is the engine while under storage?
Forced Grounding Due to Covid-19
A reality of the modern world is our ability to travel across the world quickly with the help of airplanes. In the United States alone, over 16 million flights are handled yearly, carrying nearly 3 million passengers. It is a billion-dollar industry that spans the entire globe with complex manufacturing supply lines and is subject to intense border controls.
Due to the very nature of air travel, where hundreds of people are ferried to and from places, it was one of the first industries to be gravely affected by the pandemic. The highly infectious nature of COVID-19 and the confined space and travel that planes provided created a dangerous mix for the virus to spread. Countries closed down airspace and therefore shut down air travel to prevent the virus from gaining a foothold in their populations.
As a response to this, the airline industry had to find a way to protect the integrity of their billion-dollar aircraft fleets while waiting for the pandemic to subside. Thousands of planes were grounded and due to a lack of space, were constantly exposed to the weather and the outside as they stood still on the tarmac.
Steps had to be taken to keep the planes airworthy and a number of maintenance checks needed to be done to keep them safe and secure from the environment, especially the engine.
The most critical part of an airplane is the engine. It is very expensive to make and is very fragile when encountering foreign object debris. Without it, it renders the plane obsolete and is, therefore, a priority to protect.
A jet engine is a very powerful and precise machine that provides the thrust needed to lift a large aircraft into the air. Without engines, air travel would be infinitely more difficult and expensive to achieve. Because of this, its crucial parts like the engine must be protected from damage during storage or downtime.
Protecting an aircraft engine from damage may sound like a daunting task, but with the right techniques and precautions, it can be a simple process that will save you time and money.
Protecting an aircraft’s engine is a matter of making sure that these components are properly stored and maintained during downtime. By using proper covers and plugs you ensure that the engine will not come in contact with any foreign material while it’s being stored or serviced.
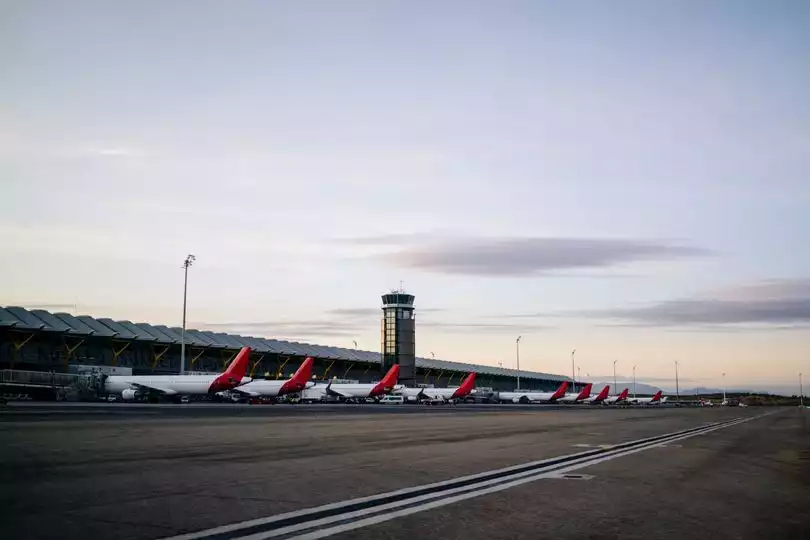
Preparing Aircraft for Long-Term Storage
The process for preparing a commercial aircraft for long-term storage is similar to the process of preparing it for use. This includes cleaning and readying an aircraft, sealing areas where there may be a risk of corrosion, and removing excess parts from the plane.
Commercial airlines typically put their planes in long-term storage during times when they are not being used especially during the pandemic. Airlines may also store aircraft in preparation for a model upgrade, such as installing new engines. Aircraft storage is typically used only when necessary and put to use quite quickly when demand requires it.
The following steps are used in preparing an aircraft for long-term storage:
- Cleaning
- Sealing areas where there may be a risk of corrosion
- Removing excess parts from the plane
Cleaning begins with removing accumulated dirt, debris, spilled liquids, and other foreign objects. This often includes removing food and drink stains from individual seats.
Commercial airlines typically seal off areas of the plane where there may be a risk of corrosion due to moisture damage. In many cases, this means closing off lavatories and galleys, as well as any compartments that may have been left open accidentally or intentionally. Moisture is the culprit when it comes to corrosion in aircraft, and any areas where moisture may accumulate must be closed off in order for the plane to remain safe and airworthy. Airlines also remove spare parts from the plane that will not be necessary during storage.
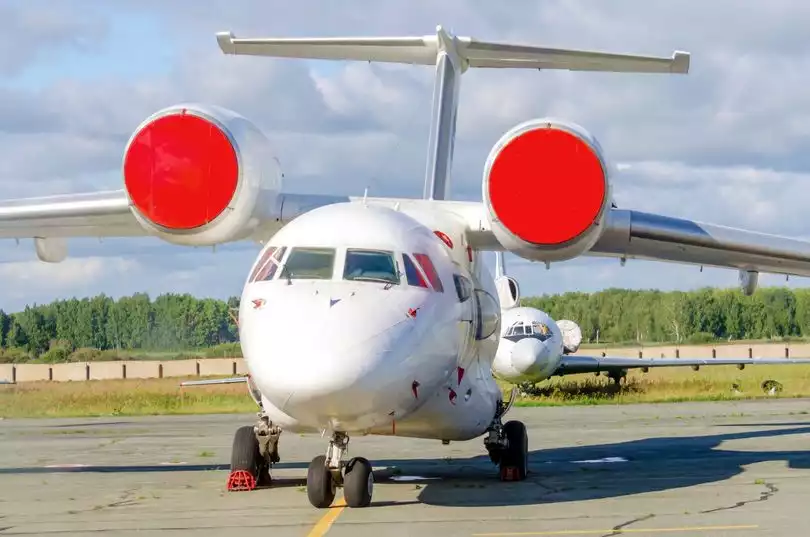
The Importance of Engine Covers
Aircraft covers are important for aircraft during storage because they keep out the elements, which can cause rust and corrosion. They are the main tools to be used in aircraft preservation.
If a jet engine cover is not used when an aircraft is put into storage, dust will be able to settle on the engine parts after a short period of time. Over a long period of time, this dirt will become acidic and could eat away at the engine parts, causing them to corrode. This is called foreign object damage or FOD.
Foreign object damage (FOD) is an aircraft susceptibility to unplanned foreign object debris (FOD), such as rocks, sand, metal scraps, parts of other vehicles, being sucked into an engine resulting in complete engine failure. FOD also includes the possibility of turbine blades being damaged when large birds are ingested into the engine.
Aircraft engines are expensive pieces of machinery, and it is important to keep them in good working order by protecting them from damage. Aircraft jet engine covers are a simple solution to a common problem that keeps an aircraft from being exposed to the elements.
There are different methods used to cover up these openings, it varies from plane to plane and manufacturer to manufacturer. There are inlet covers, pitot covers, exhaust covers, intake plugs, and exhaust plugs. When stored in a hangar, other safety measures such as fire detection systems need to be considered, since fire protection while on the ground is extremely important.
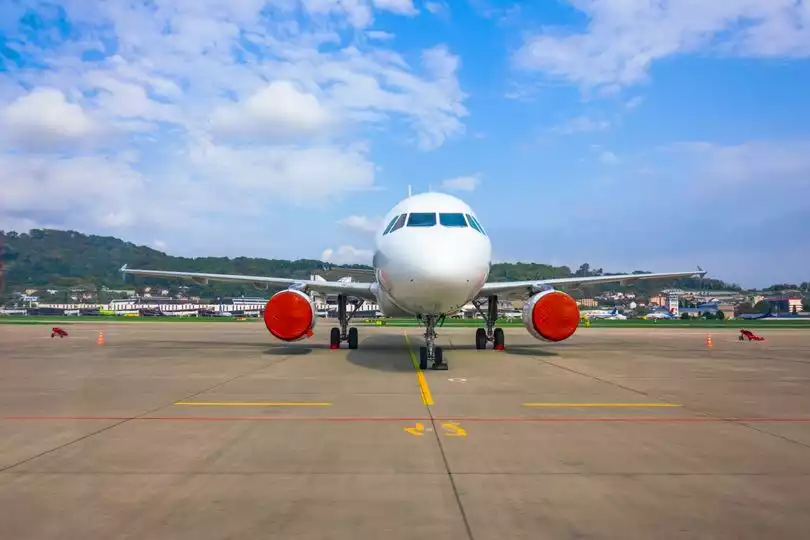
Aircraft Inlet and Exhaust Cover
During storage after landing, the inlets, and exhausts of the engines are covered so that they are not exposed to wind – these openings help cool the engine. This is why aircraft inlet and exhaust openings need to be protected
The exhaust is an area vulnerable to foreign objects. This is why exhaust covers or exhaust plugs are used to secure it safe during storage.
An intake plug or inlet cover is used to safely secure the opening of the inlet from foreign object debris.
Covers for Aircraft Tires
Aircrafts use specific heavy load tires build to resist the landings. The rubber of the tire is however sensitive to UV lights (which accelerate their aging) and to certain oils (like skydrol) often used during landing gear maintenance work. In order to extend the lifetime of the tire and to preserve its integrity without having to remove the tires entirely, airlines often choose to protect it with a special tire cover. This inexpensive method helps reduce material waste and saves manufacturers money on maintenance costs.
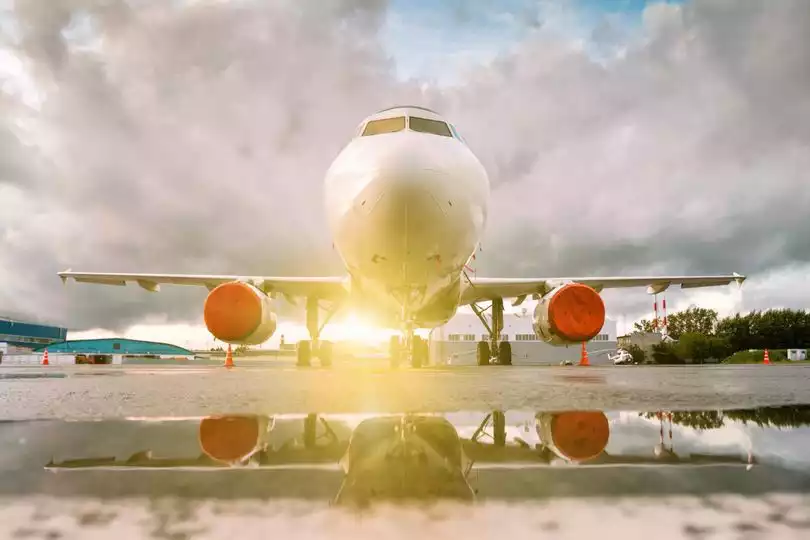
Otego Fabrics for Aircraft and Engine Covers
Otego Textile’s protective covers are a fundamental tool for the protection and maintenance of aircraft. Our flexible textile covers provide safety for your assets during the assembling process, transport, and storage.
In response to the emergency demand during the pandemic – we went into overdrive to provide our customers with much-needed covers for their fleets. Combining our worldwide supply chain and manufacturing ecosystem, we were able to deliver for our customers. Quality control was maintained to continuously produce at the highest level and still provide our customers the protection they deserve for their investments.
Otego aircraft covers are made out of our proprietary technical fabric. Highly rated and made of materials that ensure aircraft safety. The fabric was made with these factors in mind;
- Fire Resistance
- Chemical Resistance
- Mechanical Resistance
- Soft Contact
Fire resistance
Because some aircraft manufacturers recommend the storage of engine, inlet covers on board of the airplane at all time, it is crucial that the material used for such covers are safe. Our materials are fire-resistant (FAR25) and comply with airbus standard ADB0031
Chemical resistance
Different types of oil, grease, or fuel may contaminate the fabric, which can damage the cover in time.
For this reason, the fabrics used for aircraft covers need to be able to withstand many types of chemicals in order to keep out contaminants. Our materials used for aircraft protection are coated with a special polymer that enhance the resistance of the cover to chemicals.
Mechanical resistance
Since the cover has to withstand winds, rain, snow and even sandstorm, it is important that the fabric is made of resistant materials. This means that they need to be resistant to abrasion, UV, tearing, etc.
Soft Contact
Aircraft engine covers should be soft on one side to protect the engine. The material covering an aircraft’s engine needs to be strong, but also extremely flexible to allow an easy set up and removal. Our materials are lightweight, anti-scratching, heat-resistant and remain supple even in freezing temperature.
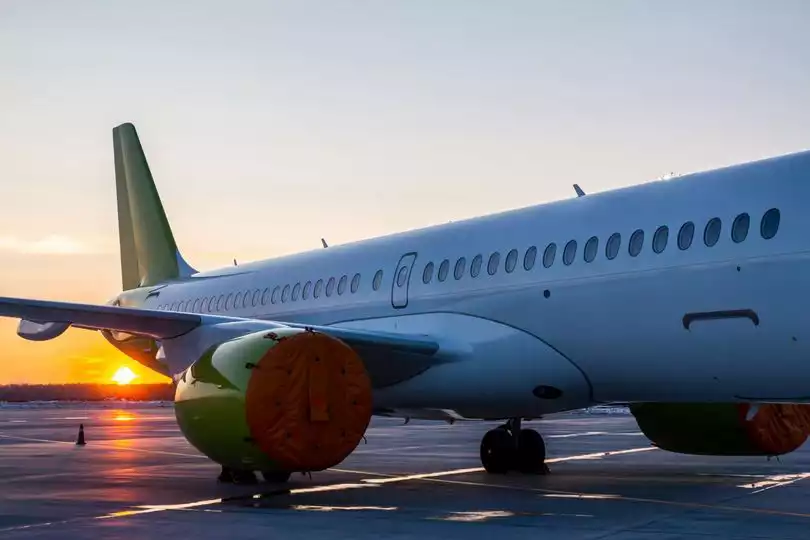
Protecting Your Aircraft With Otego
At Otego, we understand the value of your investments. Your aircraft is safe with our proprietary fabric made from the very best of materials. Our protective covers are used both in commercial and military aircrafts.
Contact us if you want to know more about the specifications of our aircraft covers.