Heat ducting plays a crucial role in many industries by controlling and directing hot air,…
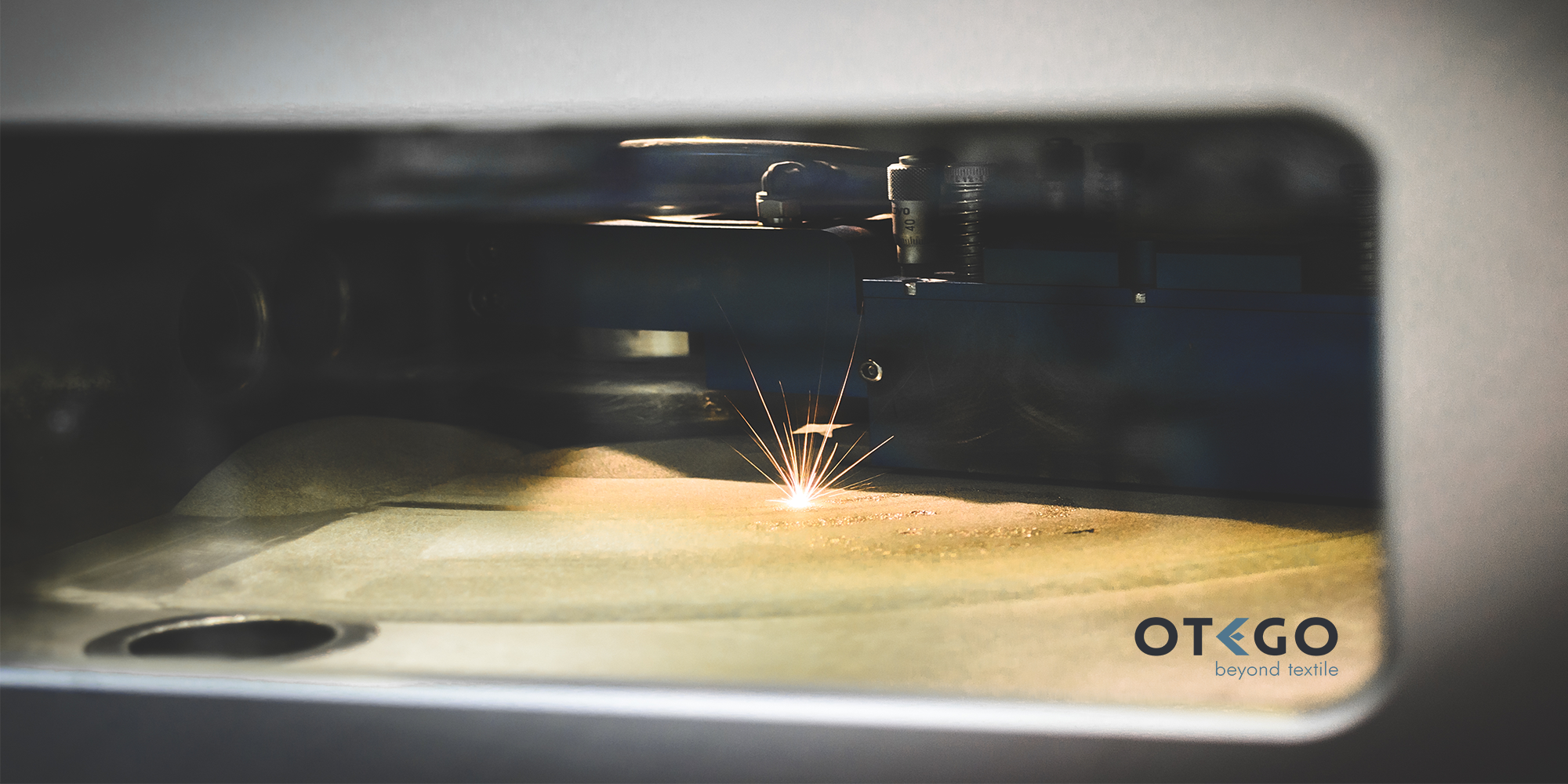
Bellows cover for 3D printing technologies
Trending in the manufacturing industry, 3D printing technologies have recently advanced to become a real keystone to produce small quantities for cheaper cost. Consuming less material, they are easy to set up and adapt to any needs. This is the perfect technology for prototyping and any project that requires custom-made high precision products such as aerospace.
Metal 3D printing
3D printing is mainly associated with light materials such as thermo plastics, but it is less known that metals (such as aluminum) can also be 3D printed using laser fusion technologies and metal powder. This allows the manufacturing of complex objects with a high precision and high durability without having to bear the initial cost of expensive molds (it can actually be used to produce molds). Thus allowing a production “on demand” of highly customizable objects.
Heat stress warping effect
The heat stress warping effect is a phenomenon caused by the expansion of the metal when heated which affects the precision of the printed object. The expansion (and subsequently its contraction during its cooling) will affect the contact point of each printing segment causing a deviation or “warp” in the shape of the object. To prevent or limit this phenomenon, the 3D printing manufacturers have introduced 3D printing machines with integrated heated build chambers.
Depending on the maker, the heated chamber can go from 180C to 350C continuously in order to slow down the cooling of the metal and allow a higher printing precision.
To protect temperature sensitive parts of the machine (such as the electronic panels, LM guides…), protective covers (bellows) will have to install.
Choosing the proper material:
Inside the heat chamber
|
Outside the heat chamber
|
|
Static cover
|
A
|
B
|
Dynamic cover
|
C
|
D
|
A.
If the protective cover is static and located inside the chamber, it is recommended to choose a reflective material made with high temperature resistant fabric (aluminized glass fabric, aluminized aramid fabric…)
B.
For a static protective cover located outside the chamber, there are fewer constraints. Any kind of fabrics can be used. Fire retardant fabrics are however recommended for fire safety reasons.
C.
For a dynamic bellow cover located inside the chamber, it is recommended to use an aluminized fabric made of aramid or carbon. Glass fabric cannot be considered because of its weakness to folding. Due to the high heat exposure, the bellow should be sewn and not welded or glued.
D.
For a bellows located outside the chamber, PVC or PU coated fabrics can be considered. PU base materials have a higher temperature resistance and can withstand occasional temperature peak up to 150C while PVC will tend to be affected around 70C. Fire resistance is also recommended for safety reasons.
Who are we ?
OTEGO is specialized into heat resistance fabrics and has developed a range of materials for bellows cover protection.